THESE STANDARDS APPLY TO RUBBER PROTECTIVE GLOVES
STANDARD-COMPLIANT PRODUCTION AND DELIVERY OF GLOVEBOX GLOVES AND PSA EQUIPMENT
Our Jugitec rubber gloves are subject to strict regulations and meet all necessary ordinances, norms and standards.
This primarily includes the PPE Regulation EU 2016/425 followed by DIN EN ISO 21420 – General requirements and test methods for protective gloves and the standards described therein:
- EN 388:2016+A1:2018
- EN ISO 374-1:2016+A1:2018
- EN 374-2:2014
- EN 374-4:2013
- EN ISO 374-5:2016
- EN 16350:2014
Further standards and test principles from our portfolio are:
- IEC 60903:2014
- GS-ET-42-1 APC 1
The PSA Verordnung EU 2016/425 sets out requirements for the design and manufacture of personal protective equipment (PPE) that ensures the protection of the health and safety of users, as well as regulations for free movement in the European Union. The many risks are classified into three categories. All Jugitec protective gloves are assigned to the highest risk category III, which requires an EU type examination followed by regular monitoring for each individual product.
PSA RISK CATEGORIES ACCORDING TO ANNEX 1 OF THE PSA REGULATION EU 2016/425
Category I includes only minor risks, such as superficial mechanical injuries, contact with weakly aggressive cleaning agents, weather conditions or contact with hot surfaces whose temperature does not exceed 50° C. The protective gloves may be tested and CE-marked by the manufacturer himself.
Category II includes all risks that are not classified as minor and cannot lead to very serious consequences. Rubber gloves in this category protect against mechanical hazards during general work with good cut, abrasion, puncture and tear resistance. They are certified by independent and accredited testing institutes. The address and number of the certification body can be found in the declaration of conformity.
Category III includes only those risks that lead to very serious consequences such as death or irreversible damage to health in connection with certain hazards, such as contact with substances and mixtures hazardous to health, harmful biological agents or ionising radiation, among others. The protective gloves have material and design-related properties that protect against certain hazards when used correctly and carefully. The marking on the protective glove shows, in addition to the CE marking, the identification number of the notified bodies that have acted in accordance with the procedure in Annex 7 or 8 of PPE Regulation EU 2016/425.
Die DIN EN ISO 21420:2020-06 specifies general requirements for test methods, labelling, wearing comfort, harmlessness to health, manufacture and design for protective gloves. The original EN420 standard has been replaced by EN21420. The new version contains additional requirements for protective gloves in the areas of harmlessness, electrostatic properties, sizes, labelling and instructions for use.
AN OVERVIEW OF THE MOST IMPORTANT REQUIREMENTS FOR PROTECTIVE GLOVES:
Harmlessness of the protective gloves: The protective glove shall be free from toxic, carcinogenic, reproductive, allergic or irritant substances. For this reason, the standard describes a series of tests that check the chemical safety of the materials used for production: Chromium(VI) content, nickel release, pH value, azo dyes, dimethylformamide (DMFa), hydrocarbons (PAH).
Hand sizes for protective gloves: The manufacturer of protective gloves provides information in the enclosed instructions for use regarding the hand sizing scheme. Each manufacturer may use its own hand size scheme.
Electrostatic properties of the protective gloves: Protective gloves with antistatic properties should be worn when working with flammable or explosive substances or powders. For the measurement of the electromagnetic properties of protective gloves, the test methods according to EN1149 are used. Protective gloves that meet these requirements may be labelled with the ESD pictogram.
Instructions for use and labelling of protective gloves: The requirements from EN420 remain unchanged. Within the framework of EN ISO 21420, supplementary information to be provided is mentioned:
- The protective gloves or at least the packaging must be labelled with a date of manufacture and (if applicable) an expiry date.
- The instructions for use contain a note on testing the protective gloves before use.
- Instructions for putting on and taking off the protective gloves.
- Declaration of the electrostatic properties of the protective gloves including a written warning indicating that an ESD risk has also been considered in all clothing and footwear worn with this glove type.
- Missing cleaning recommendations indicate that a protective glove is not suitable for washing (disposable gloves are excluded).
JUGITEC® PROTECTIVE GLOVES OFFER SAFE PROTECTION AGAINST HAZARDOUS CHEMICALS AND MICROORGANISMS
The DIN EN ISO 374-1: Terminology and performance requirements for chemical risks in the use of protective glovesIn case of contact with hazardous chemicals, they migrate through the protective glove within a certain time. The breakthrough time can vary depending on the glove polymer and the design of the rubber glove. The first part of DIN EN ISO 374 defines the performance levels 1-6, i.e. the time until chemical breakthrough. The user manual of the protective glove contains a list of the tested chemicals with the respective performance level against permeation. Furthermore, the manufacturer of the protective glove must point out in restrictive terms that – due to the individual conditions at the workplace – no information on the exact duration of protection is possible, because concrete environmental conditions such as temperature, abrasion and mechanical loads can influence the permeation time of a protective glove in different ways.
How is permeation defined for protective gloves?Permeation is the movement of a chemical through the material of the protective glove at the molecular level. Permeation includes:
- Absorption: Absorption of molecules of the chemical into the (outer) material surface of the protective glove that has been in contact with the chemical.
- Diffusion: Absorbed molecules penetrate through pores into the material.
- Desorption: Molecules escape on the opposite (inner) surface of the protective glove
List of defined test chemicals from DIN EN ISO 374-1:2018
Code letter/Test chemicals | CAS-Nr. | Class |
---|---|---|
Code letter/Test chemicals |
CAS-RN |
Class |
A Methanol |
67-56-1 |
Primary alcohol |
B Acetone |
67-64-1 |
Ketone |
C Acetonitrile |
75-05-8 |
Nitrile |
D Dichloromethane |
75-09-2 |
Chlorinated hydrocarbon |
E Carbon disulphide |
75-15-0 |
Sulphur-containing organic compound |
F Toluene |
108-88-3 |
Aromatic hydrocarbon |
G Diethylamine |
109-89-7 |
Amin |
H Tetrahydrofuran |
109-99-9 |
Heterocyclic and ether compoundsn |
I Ethyl acetate |
141-78-6 |
Ester |
J n-Heptane |
142-82-5 |
Aliphatic hydrocarbon |
K Sodium hydroxide 40% |
1310-73-2 |
Inorganic base |
L Sulphuric acid 96% |
7664-93-9 |
Inorganic acid, oxidising |
M Nitric acid 65% |
7697-37-2 |
Inorganic acid, oxidising |
N Acetic acid 99% |
64-19-7 |
Organic acid |
O Ammonia water |
1336-21-6 |
Organic base |
P Hydrogen peroxide 30% |
7722-84-1 |
Peroxide |
S Hydrofluoric acid 40% |
7664-39-3 |
Inorganic acid |
T Formaldehyde 37% |
50-00-0 |
Aldehyde |
Each protective glove/test chemical combination is classified according to the performance levels against permeation. If the permeation performance of a glove model corresponds to at least performance level 1 against at least one test chemical, it is considered to be chemical resistant.
Performance level 1 | Performance level 2 | Performance level 3 | Performance level 4 | Performance level 5 | Performance level 6 |
---|---|---|---|---|---|
> 10 min |
> 30 min |
> 60 min |
> 120 min |
> 240 min |
> 480 min |
The labelling of the glove consists of the pictogram of the Erlenmeyer flask, the number of the test standard, the identification letters and the name of the glove type. The tested chemicals are identified by their code letters and indicated below the pictogram. Eighteen test chemicals are defined in ISO 374-1. Depending on the number of chemicals tested and the performance level achieved, the following types are distinguished:
Overview of the fulfilled standards of our Jugitec B industrial safety glove
Further information on the standards can be found here
ISO 374-1/ Typ A
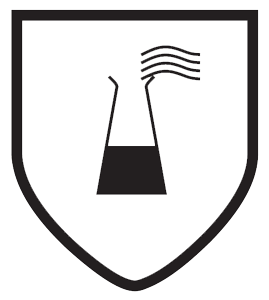
A B I K L N O T
At least performance level 2 against at least 6 test chemicals
ISO 374-1/ Typ B
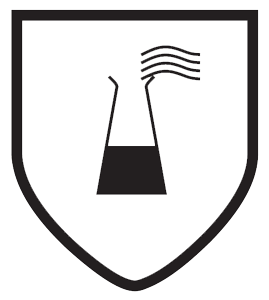
A K L P
At least performance level 2 against at least 3 test chemicaln
ISO 374-1/ Typ C
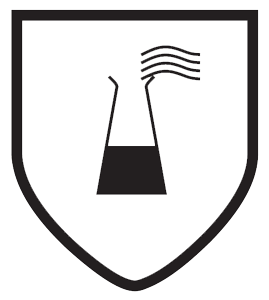
A
At least performance level 2 against at least 1 test chemical
The second part of EN 374 specifies the test method for the penetration resistance of protective gloves. Penetration is the penetration of a substance into a body. The glove is tested for the penetration of water and air into the protective glove.
EN ISO 374-4:2013 Determination of resistance to degradation of Jugitec protective gloves by chemicalsDegradation describes the physical changes in material properties caused by the action of a substance. Degradation is determined for each chemical specified in the labelling and listed in the user information.
EN ISO 374-5:2016: Terminology and performance requirements for risks from microorganismsIf the protective glove is intended to protect the end user from microorganisms (bacteria, viruses or fungi), the rubber gloves must pass the penetration test described in 374-2. Rubber gloves that provide additional protection against viruses must additionally be tested according to ISO 16604 “Determination of resistance of protective clothing materials to penetration by blood-borne pathogens”.
EN 388:2016 Mechanical risks for the safety of Jugitec protective gloves>EN 388:2016 specifies requirements for test methods and labelling for protective gloves against mechanical risks. Tests include abrasion resistance, cut resistance, tear propagation resistance and puncture resistance. A protective glove against mechanical risks must achieve performance level 1 or A for the TDM cut resistance test according to EN ISO 13997:1999 for at least one of the properties.
Testing | Performance level | |||||
---|---|---|---|---|---|---|
1 |
2 |
3 |
4 |
5 |
|
|
Abrasion resistance (number of abrasion cycles)) |
100 |
500 |
2000 |
8000 |
- |
|
Coupe test: cut resistance (index) |
1,2 |
2,5 |
5,0 |
10,0 |
20,0 |
|
Tear resistance (N) |
10 |
25 |
50 |
75 |
- |
|
Puncture resistance (N) |
20 |
60 |
100 |
150 |
- |
|
Testing |
Performance level for materials tested according to EN ISO 13997a |
|||||
---|---|---|---|---|---|---|
A |
B |
C |
D |
E |
F |
|
TDM: Cut resistance (N) |
2 |
5 |
10 |
15 |
22 |
30 |
EN 16350:2014 describes the minimum requirements for the electrostatic properties of protective gloves required for work involving a fire and explosion hazard. The contact resistance must be less than 1.0 ×108 Ohm (Rv < 1.0 ×108 Ω). The test is carried out at an air temperature of 23 ± 1 °C and a relative humidity of 25.
Jugitec products with the ESD pictogram are tested accordingly and protect people and product
EN 60903 applies to insulating protective gloves for live working. Live parts pose a great danger to people, which is why people in such situations should always be equipped with EN60903-compliant protective equipment. It is imperative to select the correct glove class for the appropriate stress level of the application.
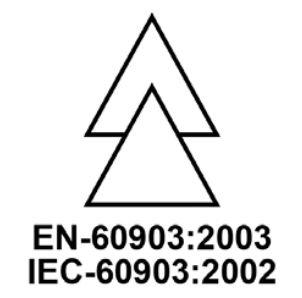
Class | Working voltage Volt | tested with ... Volt |
---|---|---|
00 |
≤ 500 |
2.500 |
0 |
≤ 1.000 |
5.000 |
1 |
≤ 7.500 |
10.000 |
2 |
≤ 17.000 |
20.000 |
3 |
≤ 26.500 |
30.000 |
4 |
≤ 36.500 |
40.000 |
Insulating protective gloves to EN60903 must also have a specified minimum level of mechanical protection and are tested for other properties such as resistance to acid, oil, ozone or extreme cold. Each glove is marked with the categories and the class they fulfil.
Category |
Additional request |
---|---|
A |
Acid resistance |
C |
Resistant to extreme cold |
H |
Oil resistance |
M |
Resistant to high mechanical stress |
R |
Resistant to acid, oil, ozone and high mechanical stresses |
Z |
Ozone resistance |
As an extension to EN 60903, GS-ET-42-1 describes additional requirements for electrical gloves worn during work where there is a risk of arcing. The tests regarding thermal protection were determined in accordance with DIN EN 61482-1-2:2015-08. In the event of an unwanted sudden electrical discharge between system parts, the user is protected from the thermal hazards of the so-called arc fault or fault arc.
Here too, it is the user's duty to check the limits and required arc classes before use in order to be able to select the correct glove.